17-4PH is a high-strength stainless steel, also known as 630 steel or S17400 steel. It is named 17-4PH because its chemical composition contains chromium (17%) and nickel (4%) and other alloying elements. It is an austenitic-martensitic stainless steel that can obtain high strength and hardness after heat treatment.
The chemical composition of 17-4PH mainly includes chromium (Cr), nickel (Ni), copper (Cu), zirconium (Zr), manganese (Mn), molybdenum (Mo), titanium (Ti) and other elements, and the proportions vary from manufacturer to manufacturer. Generally speaking, the chromium content of 17-4PH is 16.0-18.0%, the nickel content is 3.0-5.0%, and the copper content is 3.0-5.0%.
17-4PH steel is mainly used to manufacture high-strength and high-corrosion-resistant parts and components, such as aviation, aerospace, chemical industry, petroleum and other fields. Common applications include bearings, bolts, retaining rings, vibration devices, turbine blades, etc.
17-4PH steel has very good corrosion resistance and can be used stably for a long time in strong corrosive media such as seawater and oil. At the same time, it has the characteristics of high strength, high hardness and good fatigue resistance, and can maintain a long service life in extreme environments. In addition, 17-4PH also has the advantages of good wear resistance, good weldability and good processability.
The physical properties of 17-4PH mainly include density, thermal expansion coefficient, thermal conductivity, etc. The density of 17-4PH is 7.75g/cm³, the thermal expansion coefficient is 10.8-11.2×10^-6/℃, and the thermal conductivity is 15W/(m·K).
The production of 17-4PH adopts heat treatment methods, including aging heat treatment, solution heat treatment, quenching, etc. Among them, aging heat treatment is the most important step. By controlling parameters such as time and temperature, the steel can obtain the highest strength and hardness. The specific heat treatment process and parameters need to be determined according to different application scenarios and the specifications adopted by steel manufacturers.
Common Surfaces
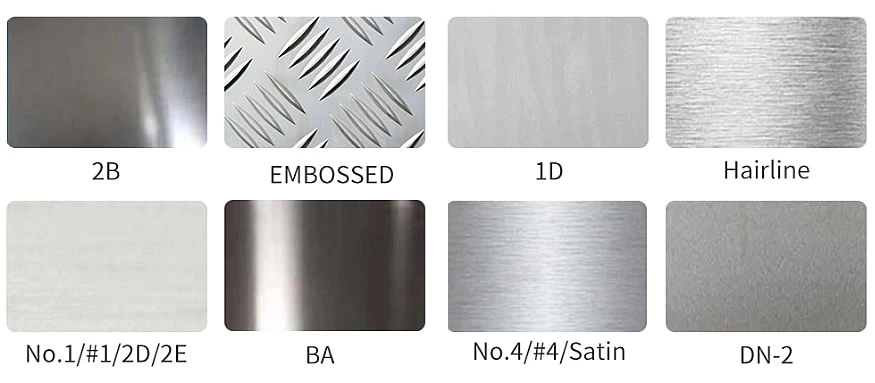
Stainless Steel Standards Comparison Table
STS |
USA |
UNS |
CHINA |
EURONORM |
RUSSIA |
SWEDISH |
JAPANESE |
GRADE |
AISI/ASTM |
NO |
GB |
NO |
NAME |
GOST |
SS |
JIS |
201 |
201 |
S20100 |
12Cr17Mn6Ni5N |
1.4372 |
- |
- |
- |
SUS 201 |
301 |
301 |
S30100 |
12Cr17Ni7 |
1.4310 |
X 12 CrNi 17 7 |
- |
2331 |
SUS 301 |
303 |
303 |
S30300 |
1Cr18Ni9MoZr |
1.4305 |
X 10 CrNiS 18 9 |
- |
2346 |
SUS 303 |
304 |
304 |
S30400 |
06Cr18Ni9 |
1.4301 |
X 6 CrNi 18 10 |
08KH18N10 06KH18N11 |
2332 |
SUS 304 |
304L |
304L |
S30403 |
022Cr19Ni10 |
1.4307 |
X 3 CrNi 18 10 |
03KH18N11 |
2352 |
SUS 304L |
316 |
316 |
S31600 |
0Cr17Ni12Mo2 |
1.4401 |
X 6 CrNiMo 17 12 2 |
- |
2347 |
SUS 316 |
316L |
316L |
S31603 |
022Cr17Ni12Mo2 |
1.4404 |
X 3 CrNiMo 17 12 2 |
- |
2348 |
SUS 316L |
316Ti |
316Ti |
S31635 |
0Cr18Ni12Mo2Ti |
1.4571 |
X 6 CrNiMoTi 17 12 2 |
08KH17N13M2T 10KH17N13M2T |
2350 |
- |
321 |
321 |
S32100 |
0Cr18Ni11Ti |
1.4541/1.4878 |
X 6 CrNiTi 18 10 |
12KH18N10T |
2337 |
SUS 321 |
347 |
347 |
S34709 |
0Cr18Ni11Nb |
1.4550 |
X 6 CrNiNb 18 10 |
- |
2338 |
SUS 347 |
309S |
309S |
S30908 |
0Cr23N13 |
1.4833 |
X 6 CrNi 22 13 |
20KH23N18 |
- |
SUS 309S |
310S |
310S |
S31008 |
06Cr25Ni20 |
1.4842 |
X 6 CrNi 25 20 |
20KH25N20S2 |
2361 |
SUS 310S |
416 |
416 |
S41600 |
Y1Cr13 |
1.4005 |
X12CrS13 |
- |
2380 |
SUS 416 |
2205 |
2205 |
S32205/S31803 |
00Cr22Ni5Mo3N |
1.4462 |
X2CrNiMoN22-5-3 |
02Ch22N5AM2 |
2377 |
SUS 329J3L |
2507 |
2507 |
S32750 |
00Cr25Ni7Mo4N |
1.4410 |
X 2 CrNiMoN 25-7-4 |
- |
- |
- |
904L |
904L |
N08904 |
- |
1.4539 |
- |
- |
- |
- |
254SMO |
254SMO |
S31254 |
- |
1.4547 |
X1CrNiMoCuN20-18-7 |
- |
2378 |
- |
253MA |
253MA |
S30815 |
- |
1.4835 |
X9CrNiSiNCe21-11-2 |
- |
2368 |
- |
17-4PH/630 |
17-4PH/630 |
S17400 |
0Cr17Ni4Cu4Nb |
1.4542 |
X5CrNiCuNb16-4 |
05Ch16N4D2B |
- |
SUS630 |