UNS S35315 redefines thermal endurance with its silicon-augmented austenitic stainless steel matrix, engineered to withstand continuous operation at 1.150°C—surpassing conventional stainless grades by 200°C. Its proprietary Cr-Si-Mn-N alloy design forms a self-repairing SiO₂-rich oxide layer, outperforming 309S and 314 in carburization, sulfidation, and cyclic oxidation resistance for next-gen emission control and heat treatment systems.
Global Certifications & Industry Approvals
Standard | Code | Specialty Compliance |
---|
ASTM A276/A959 | S35315 | ASME Boiler Code Case 2728 |
EN 10088-3 | 1.4835 | Euro 7 Automotive Exhaust Certification |
JIS G4311 | SUH353 | Japanese Industrial Furnace Standard |
AMS 5536 Rev. D | - | Aerospace Heat Exchanger Approval |
TUV Rheinland | FD 563 | Hydrogen Combustion Chamber Compliance |
Material Intelligence
Elemental Synergy
Component | Role |
---|
Silicon (1.4–2.0%) | Forms glassy SiO₂ barrier against carburizing gases |
Chromium (20–22%) | Base oxidation resistance up to 1.000°C |
Nitrogen (0.15–0.25%) | Stabilizes austenite, enhances creep strength |
Cerium (0.05–0.15%) | Refines oxide scale adhesion in cyclic heating |
Thermal Mastery
Maximum Service Temp: 1.150°C (Continuous) / 1.300°C (Intermittent)
Thermal Expansion: 18.5 μm/m·K (20–1.000°C) – 15% lower than 309S
Thermal Fatigue: Survives 5.000+ cycles (ΔT=800°C) without crack propagation
Performance Benchmark
Challenge | S35315 Solution | Validation |
---|
Carburizing Atmospheres | <0.1 mm/year penetration in 1.050°C C₃H₈ | ASTM G79 Method B |
Sulfur Attack | 0.02 mm/yr loss in 2% H₂S @ 900°C | NACE TM0177-2016 |
Hot Strength | 120 MPa creep rupture (1.000°C/10.000h) | ISO 204:2018 |
Formability | 45% elongation at 800°C (hot forging) | Automotive bellows production proven |
5 Industrial Breakthroughs
Emission Control Evolution
Enables ultra-thin 0.8mm exhaust manifolds (Euro 7 compliance) vs. 1.5mm for 309S.
Hydrogen Combustion Ready
Zero hydrogen embrittlement at 850°C/50 bar H₂ (SAE J2579 validated).
Waste Heat Recovery
92% thermal efficiency in 1.000°C exhaust gas recuperators.
Chemical Resistance
Withstands molten nitrate salts (Solar Salt CSP systems).
Cost-Effective Alternative
30% lower lifecycle cost vs. nickel-based alloys in furnace fixtures.
Cross-Sector Innovation
Industry | Transformative Applications |
---|
Automotive | Turbocharger housings, SCR catalyst cans |
Energy Generation | Biomass boiler tubes, hydrogen burner nozzles |
Metal Processing | Annealing furnace rollers, galvanizing pots |
Chemical | Pyrolysis reactors, sulfur recovery units |
Aerospace | Afterburner components, CMC manufacturing tools |
Technical Expertise Center
Q1: Welding procedure for exhaust systems?
A: Use ER353 filler with pulsed GTAW; post-weld heat treat at 1.050°C/1h for oxide layer regeneration.
Q2: Surface treatment for cyclic heating?
A: Laser-shock peening (LSP) improves thermal fatigue life by 40% (SAE AMS 2546 compliant).
Q3: Comparison to Alloy 800H?
A: S35315 offers 20% better oxidation resistance above 900°C but lower nickel content (cost advantage).
Q4: Cold-forming limitations?
A: Achieve 25% cold reduction without cracking; anneal at 1.100°C for severe forming.
Q5: Traceability for automotive?
A: Full IATF 16949 compliance with digital twin metallurgical reports.
Strategic Procurement Benefits
Automotive-Grade Supply
AI-controlled rolling for ±0.02mm thickness tolerance.
Global Stock Network
Immediate access to 0.5–25mm thickness in Detroit, Stuttgart, and Shanghai hubs.
Value-Added Services
Hot-rolled pickling, vacuum annealed finish, custom slitting.
Keywords: UNS S35315. Silicon-Enhanced Stainless Steel, Automotive Exhaust Alloy, High-Temperature Oxidation Resistant, Alloy 353MA Equivalent.
Common Surfaces
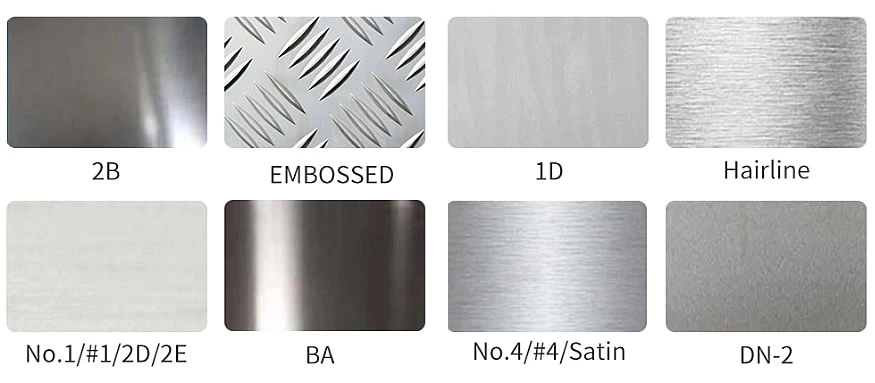
Stainless Steel Standards Comparison Table
STS |
USA |
UNS |
CHINA |
EURONORM |
RUSSIA |
SWEDISH |
JAPANESE |
GRADE |
AISI/ASTM |
NO |
GB |
NO |
NAME |
GOST |
SS |
JIS |
201 |
201 |
S20100 |
12Cr17Mn6Ni5N |
1.4372 |
- |
- |
- |
SUS 201 |
301 |
301 |
S30100 |
12Cr17Ni7 |
1.4310 |
X 12 CrNi 17 7 |
- |
2331 |
SUS 301 |
303 |
303 |
S30300 |
1Cr18Ni9MoZr |
1.4305 |
X 10 CrNiS 18 9 |
- |
2346 |
SUS 303 |
304 |
304 |
S30400 |
06Cr18Ni9 |
1.4301 |
X 6 CrNi 18 10 |
08KH18N10 06KH18N11 |
2332 |
SUS 304 |
304L |
304L |
S30403 |
022Cr19Ni10 |
1.4307 |
X 3 CrNi 18 10 |
03KH18N11 |
2352 |
SUS 304L |
316 |
316 |
S31600 |
0Cr17Ni12Mo2 |
1.4401 |
X 6 CrNiMo 17 12 2 |
- |
2347 |
SUS 316 |
316L |
316L |
S31603 |
022Cr17Ni12Mo2 |
1.4404 |
X 3 CrNiMo 17 12 2 |
- |
2348 |
SUS 316L |
316Ti |
316Ti |
S31635 |
0Cr18Ni12Mo2Ti |
1.4571 |
X 6 CrNiMoTi 17 12 2 |
08KH17N13M2T 10KH17N13M2T |
2350 |
- |
321 |
321 |
S32100 |
0Cr18Ni11Ti |
1.4541/1.4878 |
X 6 CrNiTi 18 10 |
12KH18N10T |
2337 |
SUS 321 |
347 |
347 |
S34709 |
0Cr18Ni11Nb |
1.4550 |
X 6 CrNiNb 18 10 |
- |
2338 |
SUS 347 |
309S |
309S |
S30908 |
0Cr23N13 |
1.4833 |
X 6 CrNi 22 13 |
20KH23N18 |
- |
SUS 309S |
310S |
310S |
S31008 |
06Cr25Ni20 |
1.4842 |
X 6 CrNi 25 20 |
20KH25N20S2 |
2361 |
SUS 310S |
416 |
416 |
S41600 |
Y1Cr13 |
1.4005 |
X12CrS13 |
- |
2380 |
SUS 416 |
2205 |
2205 |
S32205/S31803 |
00Cr22Ni5Mo3N |
1.4462 |
X2CrNiMoN22-5-3 |
02Ch22N5AM2 |
2377 |
SUS 329J3L |
2507 |
2507 |
S32750 |
00Cr25Ni7Mo4N |
1.4410 |
X 2 CrNiMoN 25-7-4 |
- |
- |
- |
904L |
904L |
N08904 |
- |
1.4539 |
- |
- |
- |
- |
254SMO |
254SMO |
S31254 |
- |
1.4547 |
X1CrNiMoCuN20-18-7 |
- |
2378 |
- |
253MA |
253MA |
S30815 |
- |
1.4835 |
X9CrNiSiNCe21-11-2 |
- |
2368 |
- |
17-4PH/630 |
17-4PH/630 |
S17400 |
0Cr17Ni4Cu4Nb |
1.4542 |
X5CrNiCuNb16-4 |
05Ch16N4D2B |
- |
SUS630 |